of the Supply Chain
Value chains under pressure from external factors
Demanding high performance to maintain a strong competitive edge
-
Fragile supply and distribution chains
-
Complex, constantly reconfiguring flows
-
Severe pressure on resources
-
Increasingly volatile demand
-
New requirements or regulations linked to the ecological transition
-
Focus on availability and therefore on sales, which are less and less guaranteed
-
Improving stock quality to deal with both the risk of stock-outs and the risk of obsolescence
-
Staying competitive in spite of everything :
- Being agile while keeping costs under control,
- With serene, efficient teams! -
Produce nothing unnecessary
Reduce high-impact transport
Sustainable teams
Value chains under pressure from external factors
-
Fragile supply and distribution chains
-
Complex, constantly reconfiguring flows
-
Severe pressure on resources
-
Increasingly volatile demand
-
New requirements or regulations linked to the ecological transition
Demanding high performance to maintain a strong competitive edge
-
Focus on availability and therefore on sales, which are less and less guaranteed
-
Improving stock quality to deal with both the risk of stock-outs and the risk of obsolescence
-
Staying competitive in spite of everything :
- Being agile while keeping costs under control,
- With serene, efficient teams! -
Produce nothing unnecessary
Reduce high-impact transport
Sustainable teams
The MRP is
on / off
each order movement triggers an alert, without the consequences or severity being identifiable
The MRP has
one signal only
and forces an impossible trade-off between “building a realistic plan and losing priorities”; or “keeping priorities and not knowing when products will be delivered“
The MRP is
sequential
an upward or downward movement in demand can take weeks to be perceived at the other end of the chain, severely limiting agility
Connect each Supply Chain player to the “real demand”, that of the end customer
In concrete terms, this means providing each actor involved in the flow with the information - the signal - of what he “Must-Do” to satisfy the customer's request, independently of what the others are going to do
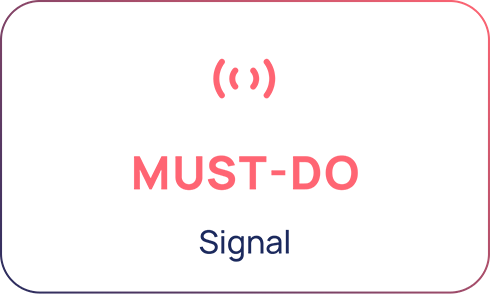
Operations are planned on the basis of this “Must-Do” signal
Everyone instantly has the same vision of priorities, being connected to customer demand
Each person acts in parallel at his or her own level to remove constraints, whether in terms of capacity or supply: the overall constraint is thus broken down into as many individual actions
Everyone understands the meaning of their actions and their impact on the end customer
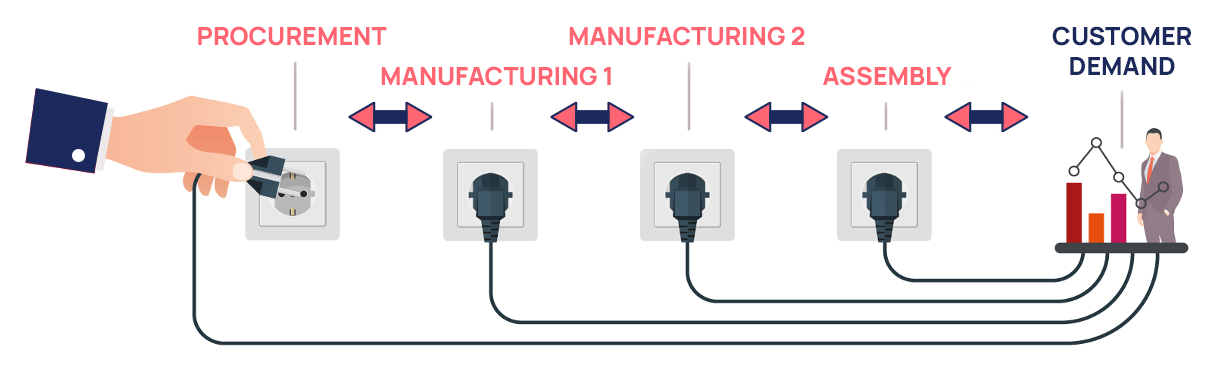
The ”Must-Do” is not on/off signal as the MRP, it consists of two dates to manage the level of priority
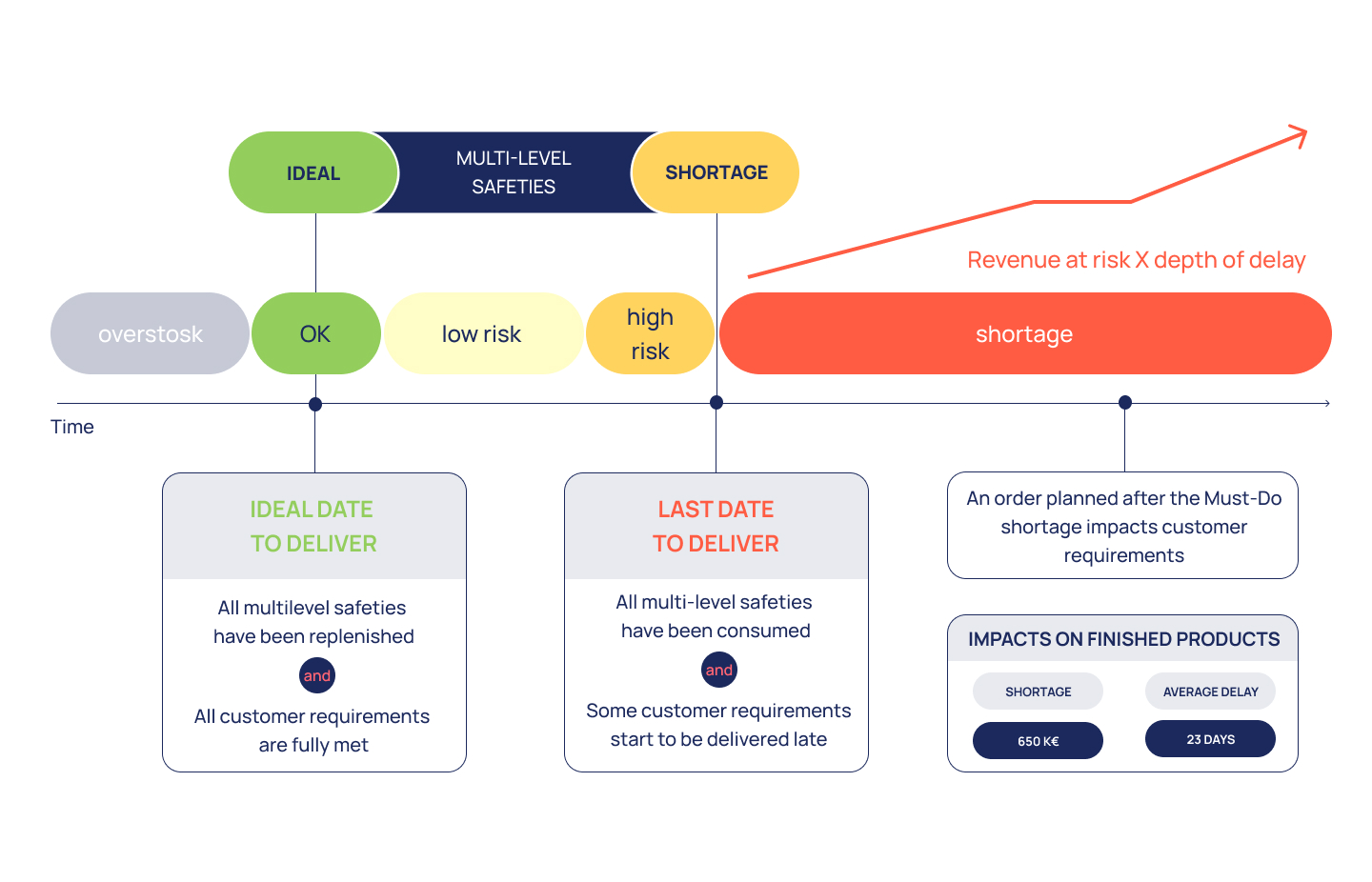
Provide visibility on what the Upstream Supply Chain is actually capable of doing, given capacity and component constraints
This principle is materialized by a second signal called “Can Do”
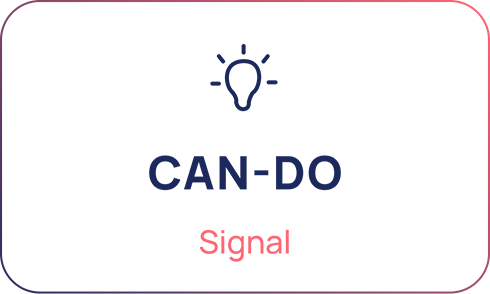
The organization is able to monitor its level of response to customer demand at all times
Each link in the chain can also see its level of contribution to the unserved demand, and can therefore take informed action to remedy the situation
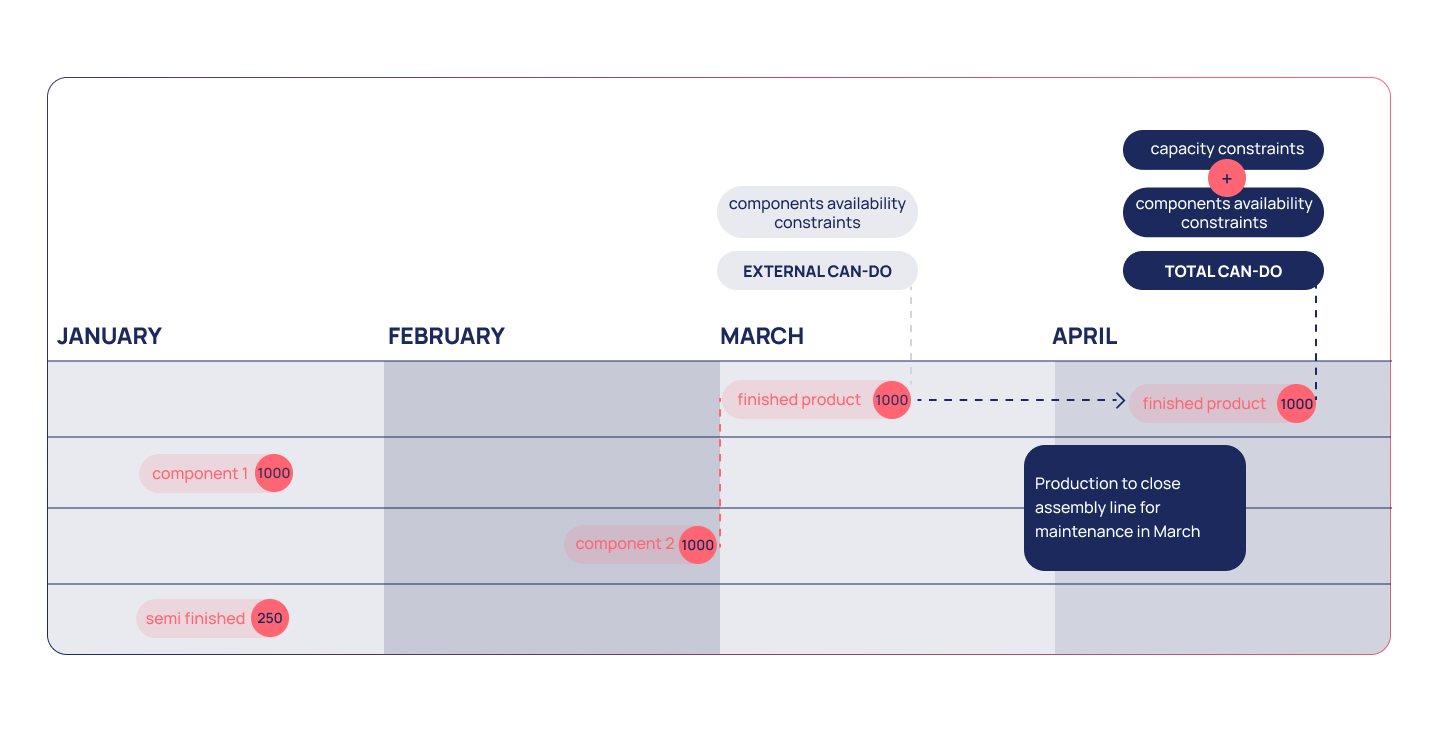
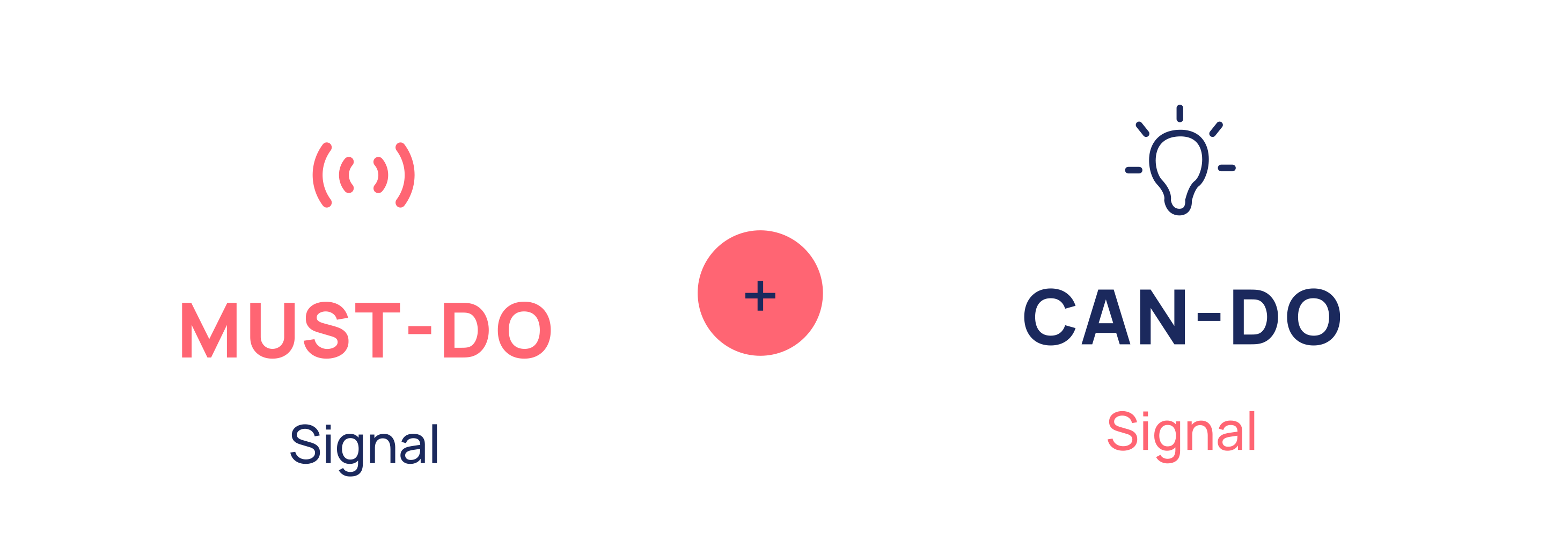
No Chain Planning fills the gaps left by the MRP, providing the agility needed to meet demand and avoid unnecessary overstocking and instability
The MRP is on / off
The Must-Do Allows all stakeholders to focus on the right priorities.
The MRP has one signal only
2 signals are available at all times: Must-Do and Can-Do. We simultaneously manage the feasibility of the plan and customer priorities.
The MRP is sequential
Thanks to Must-Do, a change in customer demand is instantly propagated to all parties in the supply chain, resulting in a more responsive supply chain.
Concrete impacts on processes






Stabilization of plans and a shared vision of the same signal also generate gains in efficiency and peace of mind for operational teams.
Service
revenue at risk reduction
Stock
inventory reduction
Cost
Ramp-up scalability without extra resources
Sustainability
Reduction in obsolescence costs
Request a
personalized demo
Contact us to start the transformation of your Supply Chain